Metodologie di riordino nella produzione
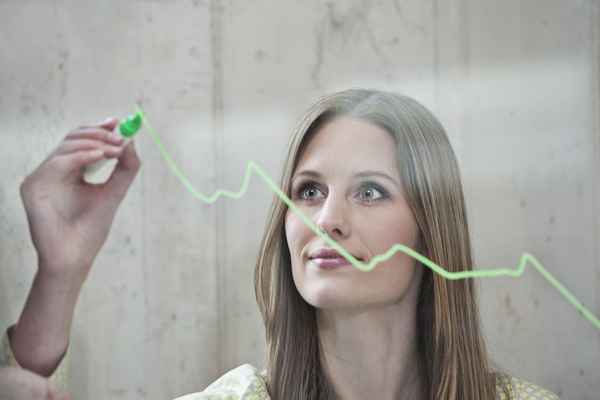
- 4649
- 149
- Alessio Gentile
Un'attività cruciale per i pianificatori è quando decidere di effettuare un ordine. Esistono una serie di metodologie di riordino che possono essere adottate. Sebbene la maggior parte dei sistemi informatici si basino sul metodo MRP di pianificazione dei requisiti dei materiali (MRP), ci sono altri metodi che i pianificatori possono utilizzare.
Metodo del punto di riordino
Questo metodo si basa sul principio secondo cui l'ordine deve verificarsi in un momento specifico in cui gli articoli verranno ricevuti appena prima di un livello di inventario che scende al di sotto del livello di stock di sicurezza. Con questo metodo lo stock di sicurezza non viene mai affrontato. Affinché questo metodo abbia successo, il livello delle scorte di sicurezza deve essere significativamente abbastanza elevato da annullare qualsiasi rischio di un magazzino, ma non essere a un livello in cui il costo del trasporto dello stock è proibitivo. Il calcolo utilizzato per il metodo del punto di riordino è il seguente:
- Riordino punto = (utilizzo giornaliero previsto x giorni di consegna) + stock di sicurezza
Ci sono tre scenari che possono verificarsi, la domanda effettiva corrisponde alla previsione, la domanda supera la previsione o la domanda è inferiore alla previsione.
Quando la domanda è maggiore della previsione, c'è un rischio di scorta o almeno che le azioni di sicurezza saranno parzialmente utilizzate. Se l'uso effettivo del materiale è maggiore della previsione, il punto di riordino verrà raggiunto molto prima del previsto e lo stock di sicurezza verrà esaurito.
A seconda del tasso di consumo, è possibile che lo stock di sicurezza sia esaurito prima che l'ordine di rifornimento sia evaio e potrebbe verificarsi un stockout. Ciò provoca altri problemi come la determinazione dell'uso quotidiano previsto.
Se il pianificatore decide che l'aumento della domanda non è un'anomalia ma la vera natura della domanda in futuro, allora la previsione dovrà essere modificata per riflettere questo. Questo a sua volta cambierà il punto di riordino. Il pianificatore deve inoltre prendere in considerazione l'idea di aumentare il livello di sicurezza o ridurre i tempi di consegna per il rifornimento.
Quando la domanda è uguale alla previsione, verrà raggiunto il punto di riordino e un ordine procedeva. Il materiale ordinato arriverà e verrà inserito in un inventario mentre il livello del materiale si avvicina al livello delle scorte di sicurezza. Sebbene è improbabile che si verifichi sempre questo scenario, i pianificatori mirano ad avere la domanda abbastanza vicina da non causare problemi importanti.
Quando la domanda è inferiore alla previsione, il punto di riordino non sarà raggiunto nel tempo previsto. Quando l'ordine viene elaborato, il livello di inventario effettivo non raggiungerà i livelli di sicurezza prima dell'arrivo dell'ordine di rifornimento. Ciò causerà quindi un picco di inventario e ci saranno costi associati al trasporto di un inventario eccessivo. I pianificatori possono provare a ritardare la data dell'ordine per gli elementi o ritardare la ricezione dell'ordine.
Metodo del punto di ordine graduale del tempo
Questo metodo differisce dal metodo del punto di riordino in quanto consente ai pianificatori di apportare emendamenti alla domanda dipendente, come promozioni di vendita, tendenze stagionali e requisiti particolari del cliente. Il calcolo utilizzato per questo metodo è il seguente;
- Punto d'ordine in fase di tempo = domanda indipendente durante i tempi di consegna + domanda dipendente durante i tempi di consegna + stock di sicurezza
Due cestino
Questo metodo richiede è una versione manuale della tecnica del punto di riordino. La tecnica dei due bidoni richiede che ci siano due bidoni. Il primo bidone contiene una quantità di materiale che può essere utilizzato senza alcun ordinamento di rifornimento.
Il secondo cestino contiene il materiale necessario durante il tempo di consegna per l'ordine di rifornimento più qualsiasi stock di sicurezza. Quando viene ricevuto l'ordine di rifornimento, il materiale è diviso in due quantità per i due contenitori e il processo ricomincia.
Ricorda, dovresti ottimizzare la tua catena di approvvigionamento in modo che ti aiuti a spedire i tuoi clienti ciò che i tuoi clienti desiderano. E spedire ai tuoi clienti quando i tuoi clienti vogliono spedire i loro ordini. E farlo fare spendendo il minor denaro possibile. Ottimizzazione quando il riordini fa molto per raggiungere quegli obiettivi.